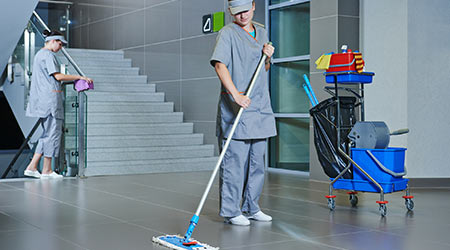
A reader writes: “We have a customer who is requiring ‘zero defects’ in maintaining one of their facilities that requires aseptic level cleaning. Any guidance would be appreciated.”
“Zero defects” was a concept developed and promoted by Phillip Crosby back in the 1980’s and has a lot of merit when it comes to manufacturing and services. It is also promoted by Six Sigma and other guides as a means of providing products and services without losses due to having to perform rework and other waste. In manufacturing products, zero defects can be documented after the item has been produced without concern for time frames in most cases.
I oftentimes use the statement that “quality does not cost; it pays” since most of us do not have overtime in our budgets to reperform work that was done incorrectly. In the scenario you are describing, zero defects references prescribed outcomes that must be performed satisfactorily each and every time. Unfortunately, in custodial operations that concept can only apply to when the work was actually performed in the given cleaning cycle. I agree with this approach since the work should be performed correctly the first time. The challenge is that if a task is performed correctly once in a 24 hour cycle (let’s say at 8:00 PM each night) what about an hour before or after the task was completed? An example is to state that the front door entrance glass is to have zero defects which can be performed if the glass doors are in good shape. The challenge is that due to traffic and use the doors will exhibit fingerprints, dust, spots and other so called “defects” during the day meaning that unless a day porter is assigned to literally clean the glass doors after each use, it will probably be soiled at some time before the next scheduled cleaning. It is very important that you clarify when and how zero defect work is to be performed and documented to avoid possible penalties. Zero defects in services must be closely tied to when the task was performed.
You need to take into account the risks associated with failing to fulfill this spec and also capture the true costs associated with it since the necessary labor and benefits may be prohibitive. It is very important that any QC process delineate the costs necessary to document the work in a timely manner. Be sure to clarify that you can achieve zero defects at the time of service but cannot be held accountable for the other 23.5 hours in the day.
Your comments and feedback are always appreciated. I hope to hear from you soon. Until then, keep it clean...
Mickey Crowe has been involved in the industry for over 35 years. He is a trainer, speaker and consultant. You can reach Mickey at 678-314-2171 or CTCG50@comcast.net.
posted on 7/18/2017