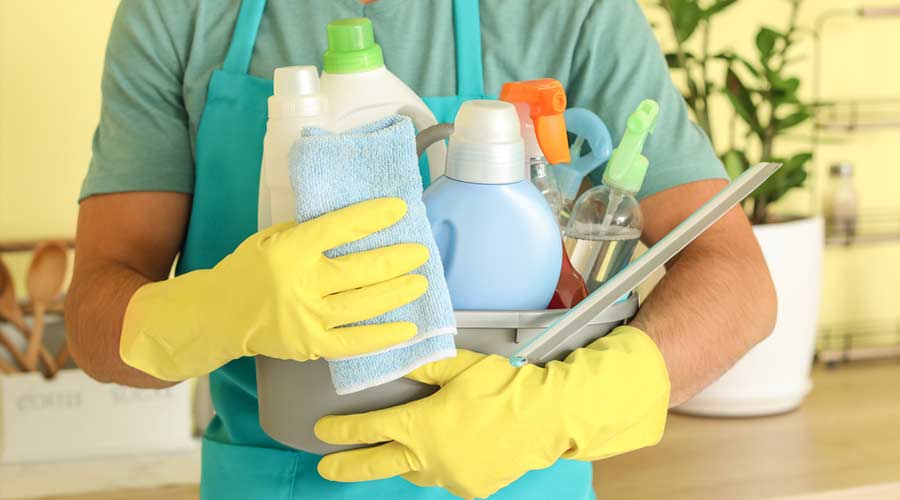
The good news for facility cleaning managers is that it’s possible to recoup at least some of the cost of surplus products that are nearing, but not yet beyond, their expiration date.
Some manufacturers offer buyback programs for certain products. They have the capacity to test and re-certify certain products, and they may be able to re-sell them depending on current demand.
There are also resale brokers that specialize in finding applications and customers for off-spec or expired chemicals.
“Obviously they purchase the distressed material at a pennies-on-the-dollar price point,” says Nathan Camire, president of AllChem Industries, Industrial Chemicals Group, Inc., a distributor headquartered in Gainesville, Florida. “But this is beneficial for both sides because physical disposal obviously comes at an additional cost, and that’s on top of the cost associated with the product value being written down to zero, or a 100-percent loss.”
Another option for recovering some costs is to devise alternative uses for overstock, so long as they’re in accordance with local regulations. For example, commercial laundry or swimming pool companies may need bleach, or car washes might be able to use certain soaps.
If there’s no one willing to purchase the products, even at a steep discount, it may be possible to donate products that are near but not yet expired to schools, shelters or churches.
“The problem is, everyone has the same issue right now,” says Halpin. “They know if they take it and don’t use it, disposing of it will cost them a lot of money. Everyone is trying to donate very similar products, and no one will take them.”
Unfortunately, in a market that’s over-saturated with expiring cleaning chemicals, disposal is often the only solution.
Facility cleaning managers should check with local waste management and water companies before tossing chemicals in the trash or dumping them down the drain. Generally, cleaning products are considered hazardous waste and require special removal procedures. It’s important to follow all regulations to avoid environmental harm and, potentially, hefty fines.
Disposal information shouldn’t be difficult to locate. Camire says it is often provided in Section 13 of a chemical’s SDS.
“If this information proves elusive for any company looking to dispose of a particular material, I’d highly advise contacting the original manufacturer of the material for guidance,” he says.
Another option is to hire a hazardous waste disposal company to safely and legally remove expired chemicals. Choose a reputable business that provides accurate documentation.
“Be very careful who you deal with and make sure to dot your ‘i’s’ and cross your ‘t’s’. Once you start disposing of it as waste, those documents stay around for a while,” says Halpin.
Disposal will cost, not recover, money. That said, it will mitigate carrying costs for unusable products and will allow managers to write down inventory for tax purposes.
Sidebar: Avoiding a Repeat Experience
During the pandemic, many facility managers moved from just-in-time to just-in-case inventory management. Rather than risk having necessary cleaning products arriving too late, they stocked up their storage rooms to have plenty of extra on hand.
After the hassle of offloading the excess, managers may be revisiting how to best manage inventory. The best practice, says Ben Walker, COO at Salt Lake City-based ManageMen, Inc., is to implement a two-order inventory cycle, or double the usage. This requires an understanding of how much of each product is required to clean each day.
“Most organizations can’t tell you that,” says Walker. “They can tell you their daily purchase based on budget, but not what they are actually using.”
Knowing exactly how many chemicals are in use allows facility cleaning managers to forecast needs and implement a predictable inventory purchasing program.
“You order when you’re finishing one delivery,” says Walker. “This way, inventory arrives just as it’s running down to the minimum of one order, to get you back to the maximum of two.”
In addition to streamlining inventory management, it’s important to streamline the products themselves. Consolidating inventory reduces redundancy costs, as well as potentially hazardous chemical confusion.
In most cases, the janitorial closet should include an all-purpose cleaner, a germicidal cleaner, a neutral mopping cleaner, and a glass cleaner. Take inventory each year, and sell, donate or dispose of expired materials.
“Pick one thing for one use and stick with that across the organization,” says Walker.
Finally, avoid the temptation to buy in bulk just to use up a budget surplus. If departments must, however, stick to daily-use chemicals that rotate more quickly through the inventory.
“It’s not uncommon for me to go into a cleaning organization and find stuff sitting on a shelf that hasn’t been used in 10 years,” says Walker. “It’s usually the specialty stuff, like air fresheners or stainless-steel polish, that ends up sitting. If you can’t use it, you just end up storing it.”
Becky Mollenkamp is a business writer in Des Moines, Iowa.
When to Keep, Use or Toss Stockpiled Chemical Inventory