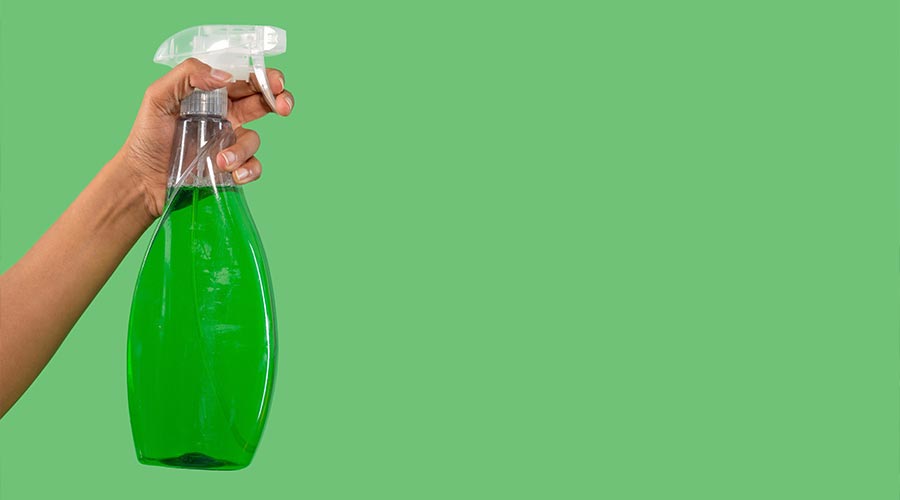
When it comes to developing a green cleaning program, there is often confusion about where and how disinfectants fit into the picture. Technically, disinfectants cannot be considered “green” because they are EPA-registered pesticides designed to kill bacteria.
“Disinfectants are a different entity. They’re the most highly regulated products in our industry,” says Herrera. “Historically, people have thought that a disinfectant, which is designed to kill germs, is contradictory to sustainability. But we’ve learned through technology and advanced formulations that there are safer ways to disinfect, and safer ingredients and chemistry that allow contractors to disinfect surfaces in a safer way for employees.”
According to distributors, customers are starting to move away from phenolic and quaternary ammonium-based disinfectants, which can potentially lead to respiratory problems or eye and skin irritation if not handled properly. Quats can also be damaging to surfaces.
“Quaternary ammonium products are safe when used correctly, but quat-based floor cleaners can leave a white buildup and dull waxed floors over time,” notes Gaskin.
Instead, a growing number of BSCs are using disinfectants that contain “greener” ingredients approved by EPA’s DfE program. These include hydrogen peroxide, citric acid, lactic acid, and alcohol.
“BSCs have to customize their disinfectant to the environment they’re cleaning,” says Gaskin. “For instance, there’s still a need for quat-based disinfectants for daily cleaning in hospitals or phenolics for treating bacteria like C. diff, but we are seeing a gradual move toward more peroxide-based disinfectants. Their kill claims have gotten more inclusive and a lot faster.”
Imperial Dade sells a hydrogen peroxide disinfectant cleaner that is safe to use on all surfaces, including glass and plexiglass. According to Rodriguez, the disinfectant allowed one of their customers to eliminate multiple cleaning products currently on hand.
“We have a county bus depot that was using nine chemicals to clean nine different surfaces on their buses,” he says. “During the pandemic, they wanted a disinfectant that wouldn’t harm any of their surfaces. So, we switched them to our peroxide-based disinfectant, which they can use on everything including plastic seats, vinyl chairs, and stainless-steel poles.”
Rodriguez points out that the damage caused by caustic cleaners and disinfectants is still evident five years after the pandemic.
“If you look throughout the U.S., you’ll see restrooms where the faucets and metal around the toilets are all pitted and rusted,” he says. “That’s because people were using disinfectants that are harsh and cannot be used on all surfaces. What we started doing as a society was to put everything on anything, which you can’t do.”
Focus on Infection Prevention
No doubt, the pandemic changed facilities’ approach to infection prevention — and BSCs responded accordingly.
“COVID-19 transformed everyone’s understanding of what a clean, healthy building environment is,” says Herrera. “It really educated our customers on the importance of cleaning and disinfecting. There’s an extra level of need now to ensure that cleaning practices and disinfection practices align with the overall wellbeing of that building.”
Rodriguez admits that during Covid, customers were less concerned about whether or not BSCs were using eco-friendly cleaning products.
“There was a need for disinfectant, and people weren’t looking at whether or not it was ‘green,’” he says. “They were more concerned about the efficacy and the dwell time.”
Today, customers’ top concern is still the spread of viruses. Fortunately, when it comes to kill claims and dwell times, disinfectants that are less harmful to people and the environment are no longer a compromise.
“During the pandemic, everything had a 10-minute dwell time. But trying to keep a surface wet for 10 minutes is challenging,” says Rodriguez. “Since then, companies have been striving to get their dwell time down, and they’ve been successful. Our hydrogen peroxide product, for instance, has a one-minute dwell time against SARS-CoV-2.”
As BSCs develop and implement sustainable cleaning practices, distributors recommend open communication with customers to keep them apprised of the products and procedures they’re using, as well as the surfaces they’re disinfecting.
“I tell contract cleaners the main thing to convey to the customer is that you have a good set of cleaning procedures,” says Gaskin. “Detail the touch points that you’re going to wipe down, how often you’re going to do it, and what you’re going to use to wipe them down. It’s really about communicating with the customer and reassuring them that you’re going to use products that are safe and that you have cleaning procedures to make sure you address all the touch points.”
Because engaging with customers and allowing them to actively participate in the process will result in a more effective green program.
Kassandra Kania is based out of Charlotte, North Carolina, and is a frequent contributor to Contracting Profits.
Navigating the Green Cleaning Landscape