High-traffic areas such as retail stores and hotel lobbies require extra effort to ensure a floor holds up under demanding conditions. Distributors can help customers maintain floors by promoting the proper programs, including those that are environmental friendly.
A Complete Program
Hard and soft surface flooring require different processes, says John Hodgkinson, vice president of sales for American Chemical & Equipment Co., Inc., Latham, N.Y.
For hard surfaces, Hodgkinson recommends a light scrub be done on a nightly, weekly, or monthly basis, depending on such factors as the weather and the number of people walking through the area. Weather causes more grit to be tracked in and causes more wear on the floor’s surface.
The floor typically should be stripped down once a year, with the scrub coat process occurring at the appropriate intervals, says Hodgkinson. For many applications, two coats of sealer and three coats of finish are sufficient, but some facilities find that they need more finish.
A high pH stripper and a neutral cleaner is recommended for scrub coats, Hodgkinson says. End users should choose a floor pad with an appropriate grit level.
When cleaning hard surface flooring, customers should use a combination of an auto scrubber and burnisher to produce and maintain the proper finish, says Fritz Gast, executive vice president of P.B. Gast & Sons in Grand Rapids, Mich.
“In a typical program the customer runs an autoscrubber over the floor with a cleaner/restorer solution that will clean the top part of the floor, soften it up a bit, and follow up behind with a burnisher,” says Gast.
High-traffic areas also require more finish than low-traffic areas, Gast says. He recommends applying several layers of finish during each cleaning, but the number of layers the cleaner lays down depends on the facility. Gast knows of grocery stores that put down 10 coats of finish during the process. The key, he says, is to extend the amount of time needed to strip the floor out.
An effective cleaning program involves both equipment and chemicals, says Hank Josephs, president of Spruce Industries Inc., Garwood, N.J. He recommends using automated equipment, which allows cleaners to cover large areas in a short period of time. These scrubbers should include automatic dispensing systems for proper application of the chemical. Various chemicals are available and should be matched appropriately to the job.
The type of floor also plays a part. Most cleaners will work on standard floors, but marble, terrazzo and vinyl require specialized chemicals.
A typical floor cleaning project has one cleaner applying the chemical (neutral cleaner or disinfectant, for example) with an automatic scrubber followed by another person operating the burnisher or polisher. The two-person team is especially important for large areas, Josephs explains.
A Green Program
In years past customers thought little about using green chemicals to clean high-traffic areas — not anymore. Now products that are both effective and environmentally-friendly are able to be used in even the busiest of areas.
Green floor-care products, including finishes and strippers, are formulated with lower amounts of volatile organic compounds (VOCs). This means less toxic fumes for cleaning workers and building occupants to breathe.
Hodgkinson appreciates that benefit and cites public data that show 20 percent of all students have a breathing disorder, with asthma being the most common ailment.
“When you’re using chemicals that are less than safe, you actually are creating an environment that can trigger an attack in an asthmatic person,” he explains.
Green products are also safer to handle because they are not corrosive to the skin or eyes. Even the packaging materials make green floor-care products safer to use. Many strippers are packaged ready to use in dilution control systems. This helps reduce accidental contact with the skin because there is less chance for spilling or splashing when diluting the product.
Green finishes are safer for the environment because they lack heavy metals such as nickel, cobalt, mercury and zinc. Zinc is used in finishes as a cross-linking mechanism to provide durability, water resistance and high-speed burnishing response. However, zinc is also toxic to aquatic life. Waste-water treatment plants and sewer districts are required by law to monitor zinc levels discharged by institutional and industrial users.
Gast says that going green means more than just a Green Seal of approval and using environmentally-friendly products.
“It is a change in cleaning philosophy that basically emphasizes the health of the building as well as the health of the people in the building,” he says.
Green chemicals have been around for years, but previously were quite expensive and didn’t seem to clean as well. Due to demand and breakthroughs in development, Gast says the cost differential now is not nearly as great and green chemicals clean as well as traditional products.
Another benefit is that many chemicals sold previously were suspect carcinogens, says Hodgkinson.
“What we’re trying to accomplish by going green is two-fold,” he explains. “To protect the environment, and also to give our employees who are cleaning the building a much safer workplace.”
If end users want to go green, then distributors should be the ones to educate them. Whether through a Web site or with factory-trained personnel, it’s important that distributors convey the benefits and value of using environmentally-friendly products.
An important component of that, Hodgkinson says, involves reviewing the Hazardous Ingredient Materials (HIMS) classification for each chemical. HIMS assigns a rating for each of three categories: health, fire and safety. The federal government tests each chemical, and provides a rating from 0 (least hazardous) to 4 (most severe). Hodgkinson says end users may be surprised when they review their HIMS information, which is found at the back of the Material Safety Data Sheet (MSDS).
Some traditional cleaning chemicals are rated 3 or 4, a point he makes when talking to customers. End users quickly realize the benefit to using green cleaners for their employees as well as their clients.
“Safety for the employee really becomes an issue when you educate the customer,” Hodgkinson says. He cautions, however, that green classification varies, and that customers should carefully review several brands before making their selection.
Some distributors feel that green floor-care chemicals will soon be the only option available.
“If [distributors] don’t go green, they won’t be around,” says Hodgkinson. “If you want to sell to a school district or to the state or federal government, you’ve got to go green,” he says. “Or you’re not going to sell them.”
The condition of the floor usually speaks volume about the cleanliness in the rest of the facility. Nowhere is that mentality put to the test more often than in high-traffic facilities. Distributors can help their customers by educating them about the proper products and procedures.
THOMAS R. FUSZARD is a business writer based in New Berlin, Wis.
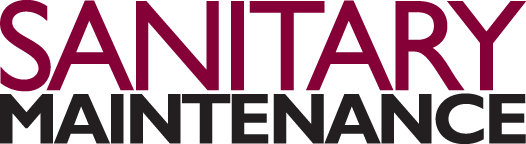
Floor-care Chemicals For The Busiest Of Areas
BY Thomas R. Fuszard
POSTED ON: 12/1/2007