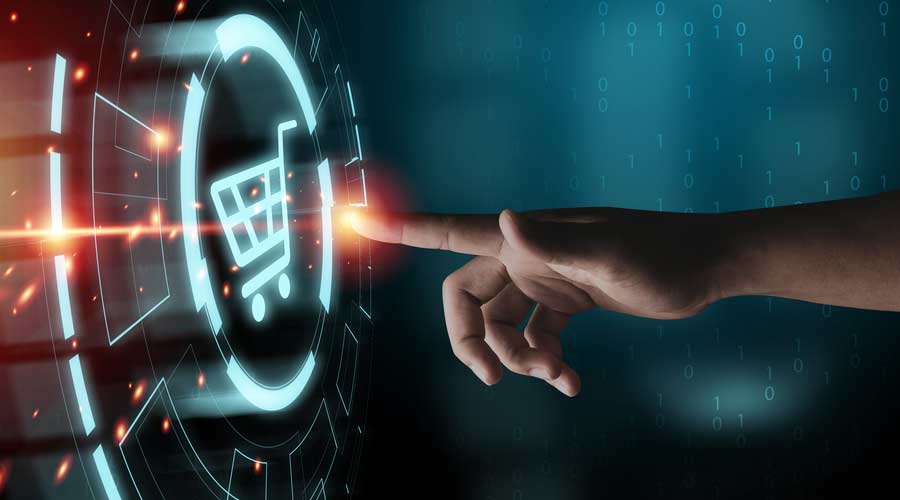
This is the first of a six-part series on the five key pillars that will drive significant, long-term improvement and enable cleaning operations to meet higher client expectations while providing the highest levels of clean, safe, healthy at the lowest overall cost.
Cleaning will never be viewed the same as it was before even during the COVID-19 pandemic. Most people have put away their masks and are attending larger indoor gatherings. And some entities will continue to discount the vital role cleaning and hygiene play in their facilities to cut costs.
However, since the pandemic, facility occupants are far less willing to work, play, heal, and live in less-than-sanitary conditions. At the same time, most organizations are eager to avoid the havoc another shutdown would have on their business. In short, the lack of cleanliness that may once have been overlooked is now a focus. Meanwhile, COVID variants, mpox, and RSV remind us that the next communal outbreak or pandemic can strike anytime.
Today’s hyper-focus on hygiene means cleaning operations must up their game. The way to do this is to look at the key areas — or the five pillars — that can drive improvement in a cleaning operation. These five steps enable in-house staff and building service contractors to meet these elevated expectations and provide the highest levels of clean, safe, healthy at the lowest overall costs.
In this series, we will look at each of these pillars, starting with the importance of improving cleaning operations — whether in-house or contracted — by welcoming emerging technologies.
Why Implement Technology
Some in the cleaning industry fear that technologies will replace workers or reduce their perceived value. The reality is that the advantages of implementing new technologies are many and can enhance a cleaning operation's actual and perceived value. Technology can help facility managers and BSCs:
• Deal with labor shortages.
• Reduce overall costs.
• Improve cleaning consistency and results.
• Increase productivity.
• Raise job satisfaction.
• Reduce the monotony of tedious jobs.
• Create free time for other essential tasks.
• Ensure better ergonomics.
• Assist an aging workforce.
• Impress stakeholders.
Depending on the technology, it can also provide data to identify where improvement might be needed and document successes.
Determine The Right Technology
Cleaning operations of all kinds need to be on the constant lookout for new technologies that can accomplish if not all, most of the above list. This requires researching, comparing and selecting the best new technologies for the specific environment being cleaned. For example, the technologies determined to be most beneficial for environmental services (EVS) teams in a healthcare environment might be different from the innovations chosen by a BSC with primarily office space clients.
Once the type of technology has been selected, the best product within each category must be chosen based on specifics such as needs, objectives, resources, and surfaces — to name a few.
Leading the Effort
Potential technologies can be assessed by a facility manager or BSC, but they can also be a team effort. What matters is that those selecting the technologies have industry knowledge and are open minded in trying new ways of doing things.
When the selection is a team effort, it is best to make clear who will make the final decision if there is no clear consensus. Manufacturer and distributor reps can also be helpful but beware of those pushing certain lines at the expense of others. Regardless of who selects the technologies to be considered, frontline workers must be included to see how the products perform in the field and to get buy-in for products selected for use.
Testing, One, Two, Three
Do not settle for product information in a pretty sales flyer or a sole product demo when it comes to testing. Request a side-by-side cleaning challenge where the new technology or product is compared to the currently used product whenever possible.
All other equipment and products used in the challenge should remain identical, and the same crew should conduct the test to ensure the comparison is apples to apples. This way the outcomes can be attributed to the product being tested.
Similarly, each challenge should have an objective, such as improving effectiveness/efficacy, productivity, or worker ergonomics. Also consider whether the products in question reduce labor, product usage or safety violations.
7 Tips for Implementing New Technologies
It can help both in-house cleaning teams and building service contractors to keep the following tips in mind when implementing new technologies.
1. Keep current. Jack Welch — the former CEO of General Electric who is regarded as one of the greatest leaders of his time — said something over 20 years ago that remains relevant today: “When the rate of change externally outpaces the rate of change internally, you will soon be disrupted and/or displaced.” Cleaning operation leaders must keep pace with the changing times.
2. Create and communicate a plan. Facility operation leaders should develop a plan that includes their objectives, strategies, and tactics for adopting new technologies and communicate it to all stakeholders.
3. Take small, consistent steps. When adopting new technologies, the cliché, “Crawl before you walk, walk before you run,” is apropos. Much time can be wasted on overly complex technologies that are “cool” but unnecessary or a poor fit for what must be accomplished.
4. Research and research some more. Dig deep beyond the marketing and sales fluff to discover the facts about any technology before considering bringing it on board. Talk to colleagues and others in the industry with expertise to learn from their knowledge and experience which technologies might be a good fit. Review as many relevant technologies as possible, and field test as many products within each category as possible.
Too often, facility managers and BSCs listen to one distributor or manufacturer. Selecting the best technology is no time for brand bias. Similarly, falling in love with one technology or product too quickly can bring on buyer’s remorse. Devote enough time to compare and test what is out there to find the product that best fills the need.
5. Ensure usefulness. Do not implement new technologies just for the sake of it. To be adopted, technology should solve a current problem or fulfill a business objective.
6. Involve all the stakeholders. The best — and often the only — way to get buy-in is to ensure those it will affect, whether through use or results, are included in the testing and decision-making process.
7. Establish and measure key performance indicators (KPIs). Measure the KPIs during the testing and after implementation to ensure the issue the technology was implemented to resolve and the metrics established to confirm success continue to be achieved.
The above explains why, when, and how it is essential for commercial cleaning operations to adapt new technologies. Stay tuned for the next in this series, where we will discuss Pillar 1 and the specific emerging technologies that must be considered to stay competitive and the correct way to use them.
Mike Sawchuk of Sawchuk Consulting is a leading education and BSC cleaning operations consultant and coach. He assists BSCs and facility management leaders, helping them improve their outcomes with insightful, pragmatic solutions and comprehensive, integrated assessments for cleaning operations. He can be reached via LinkedIn at https://www.linkedin.com/in/mikesawchuk/, or to learn more about his and his company's expertise, visit www.sawchukconsulting.com.