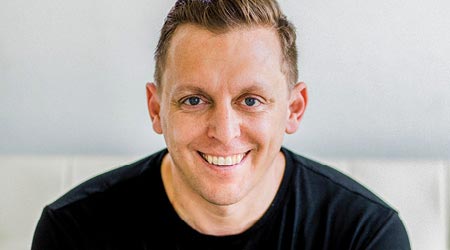
I've been chewing on whether or not to present this particular topic in this public of a forum for quite a while — not because it requires a lot of courage, but rather, it tends to get drowned out by the profound amount of noise from the supply side of the industry. Like you, I spend a significant portion of my time dealing with questions about the promises of new technology. While innovations in cleaning chemicals and equipment have definitely evolved, they are merely tools.
If we intend to elevate the craft that is professional cleaning, we must focus our attention on the standardization of cleaning operations. With all the new technology that's popping up on a yearly basis, the challenge to stay modern, while still maintaining the performance of the cleaning function, can be overwhelming. New technology, while exciting, has to be useful in all facets of an operation, otherwise it runs the risk of becoming wasteful — wasteful in time, wasteful of money, wasteful of storage space and wasteful of productivity.
I've been teaching professional development courses specific to managers and directors of cleaning operations for years. At the beginning of every course, I like to take an informal survey to determine the pressing issues that management faces on a daily basis. Standardization of the cleaning operation is consistently in the top three concerns — and a problem that everyone is trying to tackle. The question I like to follow up with is, "Why is standardization important?" The answers are also quite consistent:
Standardization eliminates waste. How much of the cleaning function in a building is waste?
One of the principal issues that cleaning managers face daily is reducing the waste in their operations. This comes in many forms and isn't always visible to the naked eye. It can present itself as a closet full of old, broken tools; repeated motion back-and-forth from storage areas; overuse of chemicals; even the actual function of "cleaning" can cause damage to the indoor environment. Since the majority of a cleaning budget is spent upon human propulsion, it is paramount to establish efficient routes and frequencies in our facilities.
Standardization promotes safety. Cleaning work can be dangerous for both cleaning workers and building occupants. A recent academic survey performed by University of California, Berkeley highlighted that the inconsistency of tasks in cleaning operations may be leading to overexertion injuries.
Having clear assignments and well-defined daily, weekly and project tasks simplify management and support safety outcomes. Most importantly, a standardized operation reduces worker fatigue because it creates a daily expectation.
Standardization creates progress. One of the primary functions of standardization is the elimination of homeostasis. Every day, when we set out to clean a building, we start at zero. Most managers don't like to admit this, but it is quite common for complaints, maintenance issues, broken tools and even daily building usage to throw an operation off course.
When this happens, the cleanliness of our buildings can suffer. This makes it difficult to not only remove the unwanted matter that was created by the building daily, but it also can create a situation where it builds up over time. Cleaning with standardized daily frequencies, tools and routes not only takes care of the dirt that came in the building today, it helps to capture what's been built up over time.
Standardization generates data. What did we use to clean the building today? What about yesterday? What's the trend? Who's following instructions? What is our process missing? What criteria are we using to measure? Is it effective? How many people do we need to achieve a clean outcome?
These are all important questions — and are often difficult for most organizations to answer. Difficult or not, standardization creates predictable patterns which help identify gaps in the cleaning program.
Standardization doesn't create perfection. This is perhaps the most important concept. Perfection rarely exists in the universe, let alone in our cleaning operations. However, standardization makes it easy to spot defects so we can correct them. It creates operational tolerances and a road map for repeatable outcomes.
Ben Walker is COO at ManageMen, Inc., a leading cleaning industry consultancy specializing in training, transitions, auditing and educational materials. In addition to his consulting work, Walker is the author of ISSA's best-selling book: 612 Cleaning Times and Tasks.