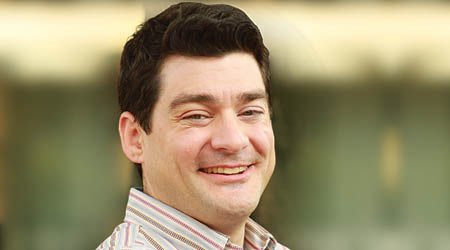
My fourth grader recently had to write something for school about the pandemic, and she decided to write about the toilet paper shortage. Apparently, that was one of the most memorable things from these past months, even though our household orders by the case of 48 rolls and I would consider other aspects of her daily life to have been more heavily impacted.
Her impression got me thinking how even with drastically fewer occupants in your buildings this year, there have probably still been shortages in your cleaning product supply chain, personal protective equipment or HVAC materials. While we haven't reached the scarcity and widespread rationing seen during World War II, your facility can still map out strategies for the foreseeable pandemic future, as well as future events.
You may already have plans in place to deal with building access and supply chain issues as a result of natural disasters (e.g., hurricanes, tornados, floods, hailstorms, wildfires, earthquakes), but those usually assume that the affected area is localized. For example, your campus might experience building damage, downed power lines or impassable roads that limit access, but other parts of the city, county or state would be unaffected and able to provide support. The challenges of a statewide, national or global event that lasts far beyond a few days or weeks makes those disaster plans a rough draft at best.
Some of the conventional supply chain thinking, as the Scarecrow would tell Dorothy, might need to be "rethunk." Consider whether it makes sense to shift from just-in-time delivery to keeping more inventory on hand, perhaps spread across multiple locations. Bundling products from a single source would historically save money and reduce shipping, but these days, a diversified supply chain provides multiple options for products that can perform the same function, but may have very different availability and pricing.
Unlike after a natural disaster, the current pandemic has left buildings structurally sound on the outside, but now require some internal modifications and procedural changes to enable a return to occupancy. The indoor air and HVAC issues are still being sorted out, but every building that's open has increased the frequency of cleaning and use of sanitizers and disinfectants. Cleaning between classes, between shifts, between appointments…between pretty much everything means that surfaces are getting cleaned more than ever before.
As a result of all the extra cleaning attention, materials are showing visible degradation. It's the facility equivalent of healthcare workers frequently washing hands and trying to avoid chapped and cracked skin. While they try to keep up with hand lotions and moisturizers, sealants and finishes in your building may also need to be reapplied more often before the bare surface is exposed and damaged. Where materials or furnishings are already damaged beyond repair, replacement products should take all the extra cleaning into consideration.
If your facility has increased spacing between furnishings in rooms, another option might be to rotate the use of rooms to reduce the frequency of cleaning, or rotate the furniture in use periodically to "even out" the wear-and-tear. Many of the sustainability concepts already in place (e.g., doing more with less, doing something differently or with a different product) can help you rethink products and processes as facility operations continue to evolve locally because of a global challenge.
Mark Petruzzi is Green Seal's former SVP of Outreach and Strategic Relations. He's in his third decade of striving for more sustainable purchasing and operations by using his engineering powers for good. He can be reached at friendlygreenguy@gmail.com.