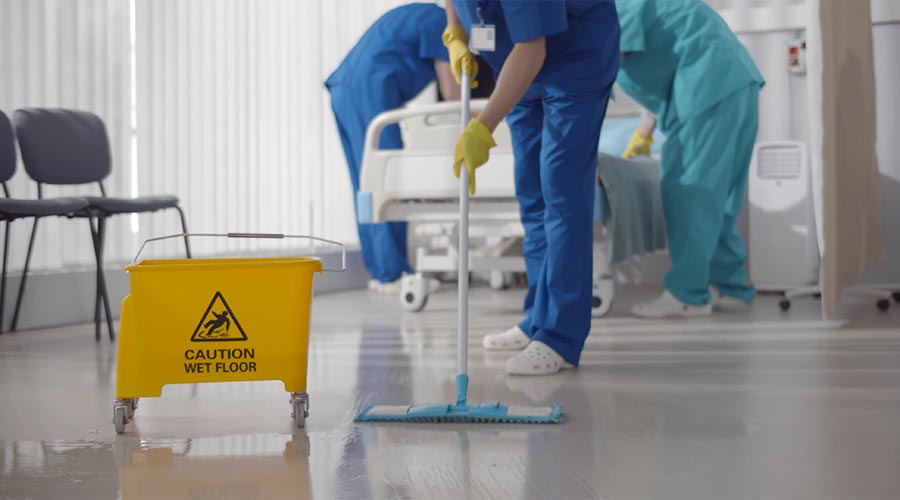
Not all mopping systems are created equal. The difference in results between mopping systems can be as clear as day, or as dirty as night.
“There are definitely some mopping systems that do a better job than others,” says Keith Schneringer, Senior Director of Marketing Jan/San and Sustainability, BradyPLUS, Las Vegas.
Schneringer asserts he can identify whether a room was cleaned with a No. 24 cotton mop or microfiber mop by just looking at it. His keen eye reveals that while a cotton mop might appear to be doing the job, it is actually spreading dirt around more than it’s picking it up.
“A cotton mop picks up the dirt and spreads it somewhere else, and every time it is dunked in the water, the water gets a little dirtier,” Schneringer explains. “After a while, you’re picking up dirt from the water and spreading it around.”
Enter microfiber. These advanced mops are more effective at trapping dirt and bacteria, but even microfiber mops can be improved upon. Craddock recommends a flat microfiber mop that is about 18 inches long and 4 inches wide. When paired with the proper bucket setup, he says this system can significantly reduce the spread of dirt.
But it’s not just about the mop — it's also about how cleaning technicians use it. Craddock says the proper technique involves using a bucket with two compartments: one for clean water and the other for dirty water.
"The microfiber mop heads should be soaking in solution, wrung out, and then placed on the floor,” he adds.
Experts also recommend swapping out mop heads every 100 square feet. And even though split-bucket systems keep water clean longer, it should be changed regularly, especially during certain times of the year.
“In summer, the water doesn’t get as dirty because mostly light soils are coming in,” Craddock explains. “But in the winter, when salt and slush are tracked in, the water will get dirty quickly.”
So, how can BSCs train workers to know when it’s time to change the water? Simple: check the color. If the water is light gray, it's still semi-clean. But if it turns brown or chocolate-colored, it’s time to replace it.
Using proper mopping techniques also makes a difference. Cleaners should start by cutting the edges of the room — cleaning around the baseboards, furniture, and any obstacles — before moving inward. They should then use a figure-eight or “S” motion while mopping to avoid repetitive strain injuries on shoulders, wrists, and elbows.
Color-coding systems also reduce pathogen spread. Many BSCs use red mops for the restroom, green mops for kitchen and break areas, and blue mops for hallways and lobbies. It’s not only important that staff be educated on the color-coding system, but building occupants should know it, too.
“If everyone knows the system and a building occupants sees a red mop being used in the breakroom, they can call us and let us know,” says Schneringer.
For those with the budget and the need for more efficiency, Schneringer recommends using mini autoscrubbers, or "micro scrubbers." These compact machines are ideal for cleaning smaller spaces, and like Craddock, Schneringer recommends automating floor cleaning whenever and wherever it makes sense.
Chemical Considerations
Proper floor care also demands the right chemicals for the task at hand. BSCs should choose options to best neutralize pathogens, maintain a safe environment, and achieve optimal results.
“If you’re working with a floor with a finish on it, use neutral pH floor cleaners,” says Schneringer. “But in a restroom, you may want something more on the acidic side to tackle the unique soils found there.”
Choosing the wrong chemical can lead to a host of issues. For instance, using an acidic cleaner on a finished floor can damage its protective layer, while using a neutral cleaner in a high-soil environment like a restroom may not be effective enough.
Another crucial element in chemical use is ensuring the proper dilution. Experts advocate for dilution control systems, which mix the correct amount of chemical with the correct amount of water, eliminating guesswork. Without these systems, cleaners often resort to the “glug method,” where they pour in more chemicals than needed, thinking it will boost cleaning power.
“What happens with the glug method is the chemical is too strong and leaves a residue on the floor,” Craddock explains.
On the flip side, under-diluting chemicals can be just as problematic. If the proper chemical concentration isn’t used, the chemical might not be strong enough to do its job, which is especially problematic in settings where disinfectant must kill as intended.
Mop and Bucket Care
The old saying, “You can’t expect to get a clean result using dirty tools,” holds true with floor care. Buckets, mops and even mop heads need cleaning.
Experts recommend rinsing out buckets at the end of each day, then tipping them upside down so that they can drain and dry. Then clean and disinfect mop handles using an all-purpose cleaner and separate disinfectant. If looped-end microfiber mops are being used, those should be laundered daily, and any synthetic or cotton mops should be thoroughly rinsed and hung to dry.
"Mops should never be left in standing water,” Schneringer adds. “That’s a breeding ground for bacteria.”
Meanwhile, if cared for properly, microfiber mops can have a long lifespan — many are good for anywhere from 500 to 1,000 washes. Despite their effectiveness and long life, some cleaning teams are still switching to single-use microfiber pads to avoid laundering altogether. While this might be a better option in facilities that lack laundry services, it comes with a higher upfront cost.
Don’t Forget to Educate
A hygienic floor care program isn’t just about keeping floors clean; it’s about using cleanliness as a powerful selling tool. Experts agree that taking the time to educate clients on the importance of proper floor care practices can make a difference in securing long-term contracts.
“When you do your initial walkthrough, ask questions to discover the pieces of equipment they have and how they’re being used,” Craddock advises. “A lot of my clients don’t know the answers to these questions or why their answers are important.”
This initial inquiry can help BSCs better understand the client’s current situation and provides an opportunity to explain specific tools and floor care methods when cleaning for health. After gathering this information, assemble a comprehensive floor care proposal that covers all necessary steps and explains exactly what will be done, how it will be done, and why it’s important.
“Share how doing these things will make a big difference in the building’s overall cleanliness,” adds Craddock. “By demonstrating knowledge and offering solutions tailored to their needs, BSCs can help clients see the value of investing in thorough, hygienic floor care.”
Ronnie Wendt is a freelance writer and owner of In Good Company Communications in Waukesha, Wisconsin.
Creating a Comprehensive Mopping System