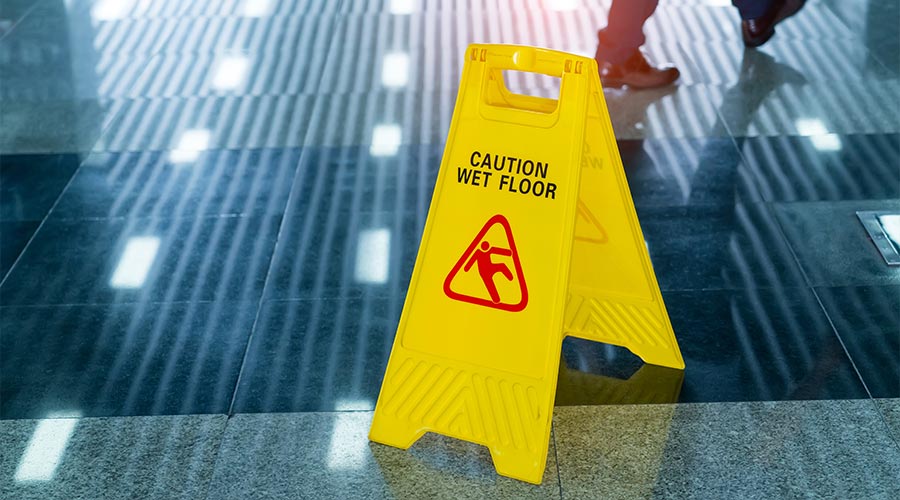
Every year, workplace injuries result in lost productivity and economic hardship for building service contractors (BSCs) and their frontline workers. As a result, liability protection policies are a must—not just to shield BSCs from litigation, but to protect employees from on-the-job injuries.
This is especially true when it comes to cleaning hard floor surfaces. Floor maintenance is one of the biggest expenditures for BSCs and their clients — and one of the most labor-intensive tasks for custodians, putting them at increased risk of injury. In fact, according to Industrial Safety & Occupational Health Markets, employees slipping on slick floors account for 85 percent of workers’ compensation claims.
“Your floor is your biggest space, and everybody uses it,” notes Rob McNealy, founder of Flooristics in Salt Lake City. “You need to have a floor safety policy in place as part of your existing workplace safety program.”
Raising Awareness
According to Bill Griffin, Cleaning Consultant Services Inc., Seattle, slips and falls are one of the most common job-related incidents, accounting for approximately 20 percent of reported injuries. Other common causes of injury related to floor maintenance involve the use of floor machinery, chemical exposure, and inadvertently mixing water and electricity.
The potential for slip-and-fall injuries is heightened in floor care, where custodians are working on wet surfaces—a risk compounded by the introduction of chemicals.
“If I were writing a policy, I would start with ‘be aware of your surroundings,’” notes Stan Hulin, president and CEO of Future Floor Technology Inc., Gladstone, Oregon. “It’s really obvious, but everyone misses it.”
Before work begins, BSCs should ensure staff are properly trained to check floors and the surrounding environment for potential factors contributing to injuries, such as broken or loose tiles, loose handrails, or poor lighting.
The introduction of detergents, surfactants, or other chemicals can also increase the potential for slip-and-fall injuries, particularly if using a stripping chemical that emulsifies floor finish, which makes floors extremely slippery. In fact, consultants concur that floor stripping is one of the most potentially hazardous floor maintenance tasks that frontline custodians can perform, which is why liability policies should detail proper stripping procedures, focusing on personal protective equipment (PPE) and outlining common-sense tips to avoid injury.
“If someone on staff falls in an acidic floor stripper it can burn them, so don’t walk in puddles,” notes McNealy. “It sounds obvious, but if you don’t tell people not to do it, they probably will. Also, don’t strip or mop yourself into a corner.”
If walking in floor stripping chemicals is unavoidable, Hulin recommends shuffling feet rather than lifting them to help lessen the chance of a slip-and-fall injury.
Just as cleaning chemicals can increase the slickness of floors, improper maintenance can reduce floor traction over time, contributing to slip-and-fall injuries. For this reason, liability policies should review general floor maintenance procedures, focusing on the importance of proper dilution ratios and prescribed cleaning systems, such as color-coded tools and two-sided buckets that promote proper rinsing.
“If you’re mopping a kitchen floor where grease splatters and then using the same mop in the dining area, you’re likely to make the floor extremely slippery,” says Griffin. “These are the kind of things you need to be aware of.”
However, floors don’t have to be wet or greasy to be slippery. Dust and soil are also culprits that can create an unsafe surface.
“Just because a floor is dry doesn’t mean it is safe,” McNealy says. “Dust on a really smooth surface can act like ball bearings or a lubricant under your feet.”
Dry floors can also lead to trip-and-fall injuries, where the floor itself is the trip hazard.
“If a floor is too tight—meaning it has too tight of a slip coefficient—it could stop your foot and cause you to stumble forward,” Hulin explains. “Make sure frontline staff doesn’t over-apply anti-slip restorers.”
Safety Barriers and PPE
Consultants agree that airtight floor safety policies should include detailed coverage of safety barriers and personal protective equipment—the most important of which is proper footwear to avoid slip-and-fall injuries and chemical exposure.
“I’ve seen severe chemical burns on people’s feet because they strip floors in tennis shoes,” says Hulin. “Make sure they know to wear appropriate foot protection.”
Options include protective overshoes with aggressive soles or abrasive pads that strap onto existing shoes. Proper footwear is also imperative when custodians are required to walk on snow or ice.
“I had a worker who grabbed the ice melter and snow shovel to clear the steps by the front door and in the process fell down because he wasn’t wearing the right shoes,” Griffin recalls. “There are spiked shoes and attachments you can put on the bottom of your shoes to walk on ice, so be aware and provide those for staff.”
Protective clothing isn’t limited to shoes, particularly when stripping floors. A slip-and-fall injury could result in chemical burns to other body parts that aren’t protected, while chemical splashes could cause burns to exposed skin and eyes. For these reasons, additional protective clothing may be required, depending on the floor cleaning task at hand.
Hulin, for example, learned the hard way the importance of wearing hand protection.
“When detailing and using sharps or putty knives, you need cut-prevention gloves,” he says. “I know this because I have a scar on my hand from not wearing protection while detailing a floor.”
Hulin was holding a razor blade in one hand while opening a door with his other hand. As he pulled the door open, it hit the razor blade, causing the blade to cut his hand.
In the past, when Hulin was responsible for managing custodians, he required them to carry a duffle bag with their own PPE. This included rubber gloves, rubber boots, safety glasses, ear plugs and an extra set of clothes, including underwear. He also required employees to carry a door stop to hold doors open when maneuvering equipment into and out of areas.
“It’s the little things that get you,” he notes.
When focused on floor safety, policies should also address the need for safety barriers to protect frontline staff as well as building occupants.
“Putting up wet floor signs is not enough,” notes Griffin. “You lessen your liability if you put up barricades. People must take action to overcome the safety protocol you put in place, and they’re not going to win in court if they say they didn’t see the tape they pushed down and stepped over.”
Experts agree that safety barriers should be used whenever hard floor maintenance is in progress. Most recommend three-inch caution tape or danger tape for stairwells, stripping floors or working around electricity. Other safety equipment may include ground-fault circuit interrupters as well as child safety plug protectors covered in duct tape for floor outlets.
Power of Prevention
Liability protection policies for floors should assess and document risks associated with different types of flooring. For example, smooth, highly polished floors, such as granite and marble, tend to have lower traction, making them more susceptible to slip-and-fall injuries.
Hazard analysis and walkway audits to determine a floor’s slip resistance are often relegated to a management team member who undergoes walkway safety training. According to Griffin, the Occupational Safety and Health Administration (OSHA) offers 10-hour and 30-hour general safety training courses, as well as a 30-hour instructor course, with classes available at regional training centers.
In addition to having a liability protection policy, consultants recommend that BSCs work closely with their clients to improve safety for frontline workers while on site. This might include a discussion of preventative measures, such as how to keep soil out of the building.
“Many times, BSCs don’t talk about this stuff with their clients, but their clients would value it,” says McNealy. “For example, I would recommend expanding walk-off matting at entrances because the less soil coming into the building, the less cleaning you have to do and the higher your traction levels, making your floors safer.”
He also suggests querying clients about walkway safety in their facilities.
“Have a conversation and ask them what they’re doing to improve walkway safety,” suggests McNealy. “As a BSC, I’d want to know: Do you have your floors traction tested or audited? Have you had a lot of slips and falls? Have you had any lawsuits? Because if it’s dangerous for customers, it’s dangerous for janitors.”
Although the onus is on BSCs to create liability protection policies that minimize dangers and reduce the risk of lawsuits, the ultimate responsibility for keeping employees safe lies with the frontline staff performing the work.
“The supervisor can’t watch employees eight hours a day,” says Griffin. “The workers must assume responsibility for their safety. We need to put more emphasis on the individual and hold them accountable. Custodians may not be safety managers, but they are the safety managers of their lives.”
Kassandra Kania is a freelance writer based in Charlotte, North Carolina, and is a frequent contributor to Contracting Profits.