Testing ProTeam's New Backpack Vacuums
Loading the player ... |
Mark Tomasiak |
In this podcast, we interview Mark Tomasiak, Manager Technical Development for Emerson Tool Company |
Q: What is Underwriters Laboratories Inc. and what do you do with them?
UL is a world-wide safety consulting and certification company. They are approved to perform safety-testing in the US by the federal agency, OSHA. We tested the safety and durability of ProTeam's Next Generation backpack vacuums in the UL-certified laboratory at Emerson World Headquarters in St. Louis.
Q: How did you end up testing ProTeam's new backpack vacuums?
We have been testing different varieties of vacuum cleaners at this lab for over 40 years. When Emerson acquired ProTeam in 2009, ProTeam had been testing their vacuums for 20+ years. So, combined, we had over six decades of experience to draw from. Together we took a look at customer feedback on ProTeam's existing top-performers and started working on making them even better. Then we had to validate that the new designs were as safe and durable as ProTeam users expect.
Q: What features did you work to improve?
Well, the ideal scenario would be a backpack vacuum that doesn't weigh anything, makes no noise, and has lots of power. In lieu of the impossible, we tried to find new ways to move even further towards those goals. When we had done everything we could to make the vacuum lighter, we made it feel lighter. When we had done everything we could to make the vacuum quieter, we made it sound quieter. We think we came up with some innovative ways to improve on an already robust design.
Q: What do you mean feel lighter?
Something we got from customer reviews was that the old models sat too far back. They pulled back on the shoulders of the user, making them more taxing to wear. In engineering terms, this is a cantilevered load. We knew we needed to move the weight as close to the body as possible - that's how the shape got to be a narrow triangle - to remove that cantilevered load. We also created more articulation in the harness to make it more responsive to the user. So it's comfortable - more like an extension of the body.
Q: And how did you make it sound quieter?
We tweaked the shape of the body to change the way sound exits the vacuum. It is aimed away from the ears of the user now, making the experience quieter for the user, and we were able to improve the user's experience without sacrificing power.
Q: So you improved upon the previous designs, then you tested for UL safety certification?
Right. We had a template for testing the safety of vacuum cleaners, both from UL and ProTeam. We used that template as a starting point and adjusted it for the new features of the Next Gen vacuums. The tests involved evaluation during normal operation, and then there are the abnormal tests where we defeat one safety feature at a time to make sure it fails in a safe manner.
Q: How was your lab equipped for these tests?
Our team used test cells to create the correct conditions for an exhaustive series of safety tests. One cell was equipped to test airflow and suction measured in cubic feet per minute (CFM) and inches of water lift. The cell we used to test burnout resistance had fire extinguishers mounted on the walls, ready to discharge at the push of a button. We used probes of different sizes to be sure that an adult's or child's finger could not fit into any part of the vacuum and touch an energized or moving part.
Q: So after the safety of the units was verified, were the vacuums ready to release to the market?
The tests did not stop with the minimum UL safety requirements; they went much further. We also had to validate the durability of the units. ProTeam backs these units with a 3-year warranty on parts, labor, and motor and lifetime warranty on the molded body parts, so we had a high bar to clear. Anywhere the new design differed from previous designs we tested more extensively.
For example, ProTeam had never used injection molded body parts on the older style backpack vacuums, so we needed to validate that they would be just as strong as the previous molded bodies. Where UL only requires a three-foot drop test, we performed a series of six-foot drops from the top of a ladder and confirmed that the vacuum still operated normally. The worse thing that happened was the HEPA filter doors would pop open.
We also simulated aging to make sure the plastic parts don't become brittle over time. We tested in 32 degrees Fahrenheit and 105 degrees Fahrenheit, so we know the backpacks will perform after being transported in winter or spending the night in a garage in Arizona. We confirmed that the motor runs over 800 hours on one set of brushes. We had to prove that the new backpacks live up to ProTeam's legendary durability, especially the new FlexFit™ articulating harness system.
Q: How did you simulate 3 years of wear on the harness system?
We took a couple of air cylinders and articulated each shoulder strap for 20,000 cycles, trying to wear out the straps. We articulated the upper pad for 20,000 cycles rotating it 30 degrees both ways trying to wear out the ball joint. We tested the carrying strap to see if it was thick enough by loading the vacuum with 25 pounds, twice the weight of the unit with 10 quarts of dirt in it, and picked it up 20,000 times. We never had a failure.
Q: At the end of this process, do you feel that you met your goals with the Next Generation backpacks?
I think so. We had people from every discipline involved in the project team – marketing, engineering, safety - and everyone had their say along the way. We proved its every bit as durable as the previous generation of backpacks, which have always been excellent. It's better looking, and we went way beyond what was required in making it comfortable, so it's easier to wear and use.
The Next Generation backpacks, the Super Coach Pro™ 10, the Super Coach Pro™ 6, are different than anything else we've seen on the market. We knew they would be game-changers for the industry, so it was exciting to be a part of this project.
posted on 9/11/2013
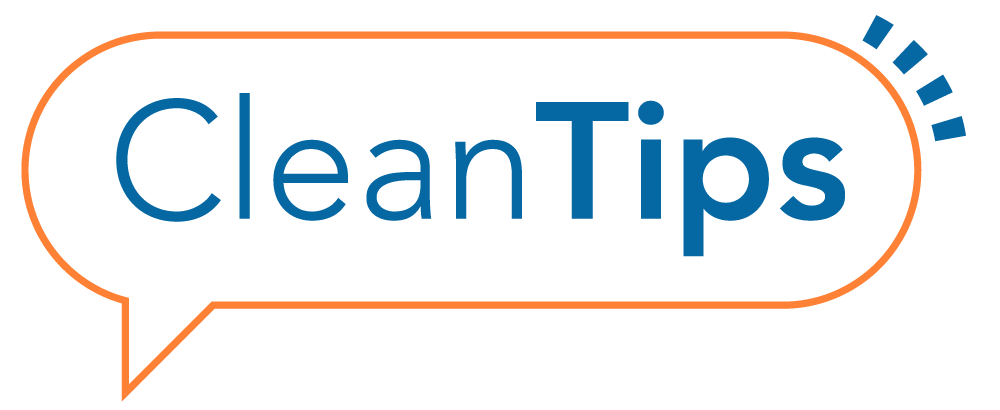