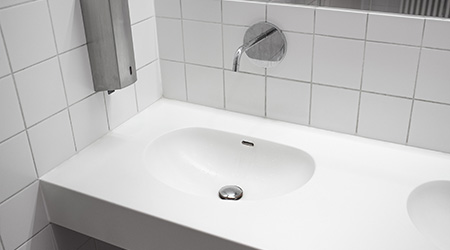
A reader writes: “Our new customer is requiring us to replace batteries in air fresheners, dispensers and other devices. We did not include the cost of labor and batteries in our bid. Can you help with suggestions?”
Based on a quick review of the specifications, you agreed to service these units. The customer did not provide a count of units (126 total), nor did they give the type batteries required (AA, AAA, C and D cells). They also failed to indicate the frequency of changing them out. You need to do the following:
- Verify the total inventory of devices that require regular inspections and change out frequency.
- For instance, it appears that the air fresheners in the rest rooms need changing at least monthly; whereas the paper towel dispensers vary by brand and frequency of use.
- You need to calculate (preferably through time studies) how long in minutes it takes to service the various units per visit.
- Don’t forget set up for those requiring a ladder or other work.
- Once you have that number, you need to annualize this into DLH (direct labor hours) which then needs to be divided into the total number of FTEs (full time equivalent) needed for this task.
- Multiply this number by your Burdened Labor Rate (wages + benefits + ???) for total.
- Then add the total annual dollar costs for the batteries.
- This total should give you a good range for estimating your annual costs.
You may find the cost of labor is more than the cost of the batteries. Unfortunately, you did not read the specifications closely, ask the right questions and include this cost in your proposal which of course, was the lowest, since your competition added this in.
Your comments and questions are important. I hope to hear from you soon. Until then, keep it clean...
Mickey Crowe has been involved in the industry for over 35 years. He is a trainer, speaker and consultant. You can reach Mickey at 678-314-2171 or CTCG50@comcast.net.
posted on 1/15/2018